Air Barriers Versus Vapor Barriers
Building a tight, secure house is more than simply building
to code. It’s a source of pride among construction professionals and a
signature element of a quality build. You want the finished structure to be
warm and dry in winter, cool and dry in summer, just right in the shifting
seasons in between and able to withstand all of those challenges long term.
So, when you’re assembling building materials and components, the ultimate goal
is to create—and keep— a neat envelope of protection shielding the home from
weather, the elements and issues that might result if the envelope weren’t in
place to do its job.
Key to that protection are air barriers and vapor barriers—two categories of
building materials that can prove confusing as concepts because they often
overlap, work together or—in some cases—do double duty. However, each has a
very specific task to address:
Air barriers block unwanted air from traveling through open spaces like cavities, gaps or cracks.
Vapor barriers block the movement or unwanted transfer of moisture through solid surfaces or materials like wood, drywall or masonry, for example.
Something to keep in mind, however, is the U.S. Department of Energy’s
often-cited observation that “air movement accounts for more than 98% of all
water vapor movement in building cavities.” This is why stopping air is the
first priority and why—when you can’t stop the infiltration of air, temperature
shifts or resulting moisture—vapor barriers also become a critical tool of
choice. It’s a matter of choosing the right barrier to counter the challenges
of the job.
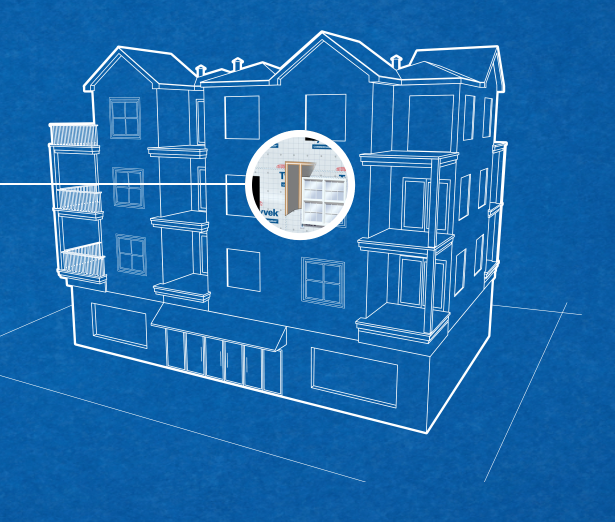
Air, Heat and Moisture Problems in Construction
When you build, your intent is to create a stable environment that is easily controlled, adjusted and maintained. Accounting for the natural behaviors of air, heat and moisture within a design is crucial to achieving that goal.
Air— Air moves quickly, constantly seeking an outlet that will release it from a high-pressure area to a lower pressure one. It can be as simple as air slipping through a gap in a door seal, for example, or an electrical outlet. However, air—still or moving—also carries with it the more complex elements of temperature and humidity.
Heat—The second law of thermodynamics governs heat transfer and the fact that warmth moves from hot objects to cooler ones until equilibrium is achieved—that is, both objects reach the same temperature. Highly conductive materials like steel, for example, allow this to happen more easily while materials with low conductivity—insulation, for example—slow or even stop the process.
Moisture—Moisture can form due to dewpoint and condensation. Depending on its temperature, air can hold varying amounts of water. Generally, the warmer the air, the more moisture it can hold. If warm, moist air is able to move to a cooler destination, it will release the moisture it can no longer hold as condensation. The temperature at which this release begins to occur is the dewpoint, often a variable that shifts with environmental conditions. What can make this especially challenging is that once moisture forms, vapor drive will cause it to spread from areas with high concentrations of moisture and saturate drier areas.
Weather, seasons, climate, geography and even altitude can directly impact the
intensity of effects like air movement, heat transfer, and condensation and
vapor drive. That’s why understanding the range of options available in
building materials and matching a home plan’s design and barrier systems to the
surrounding environmental conditions are so important.
Air Barriers
The purpose of an air barrier is to prevent air—along with the heat and
moisture that it carries—from infiltrating or escaping from a building. While
air barriers can consist of a single material, more often, they incorporate a
whole assembly of materials that together create a protective envelope that
keeps desired conditions within the envelope and undesired conditions outside
the envelope—an air barrier system.
An air barrier system can be external or internal, and most homes have
multiples thanks to accepted construction principles, but basic requirements
are the same:
It should be impermeable to air flow.
It should be continuous, without gaps, cracks, open seams or joints, or other compromising points of ventilation.
It should be structurally sound and able to withstand forces that may act upon it—wind, for example, or weight loads.
It should last the expected lifetime of the building.
Many of the most commonly used building materials serve as effective parts of
an air barrier system, securing every aspect of a home—from the roof system to
the floor system as well as the above-grade and below-grade wall systems. Air
barrier components can include everything from concrete, glass, plywood and OSB
to drywall or gypsum board, rigid or spray foam insulation, polyethylene
sheeting and rubber membranes as well as the gaskets, tapes, sealants and
adhesives needed to make a barrier truly continuous.
The term continuous is important because it bars any interruptions or
breaks—flaws that degrade air barrier performance, result in moisture damage,
provide access to pests, and increase heating and cooling costs for a home.
While flat, single-material surfaces are the most basic element of an air
barrier, areas typically requiring extra materials to interface or overlap
transitions, for example, include joints between different building materials,
angled joints or corners, and plumbing or electrical penetrations.
Vapor Barriers
The purpose of a vapor barrier is to prevent moisture from directly contacting
or moving through solid surfaces. They’re often installed in areas prone to
condensation where an air barrier alone is not enough. The idea is to protect
building materials from moisture that is likely to form. However, the use of a
vapor barrier and its placement need to work with—rather than against—the
home’s design and environmental conditions.
While a home may have a number of layered air barrier systems in a given area,
vapor barriers work solo—only one impermeable layer protecting a particular
space—and correct placement is crucial. Since condensation occurs when hot air
cools, vapor barriers typically sit on the warm side of a wall—also referred to
as the warm side of the insulation or frame wall. The idea is to stop the
movement of moisture vapor before it can reach dewpoint, condense and diffuse
into adjacent materials like insulation, for example, where it can result in
mold and water damage.
Some of the areas of a home most in need of a vapor barrier are basements,
foundations and crawlspaces as well as floors, walls and ceilings. Because
these features are perimeter interfaces delineating inside and outside, climate
is often used as a general guide for vapor barrier placement.
In warm climates, the vapor barrier is typically installed on the exterior side of the frame wall and insulation layer. With cool, air-conditioned interiors, vapor drive moves inward.
In cold climates, the vapor barrier is typically installed on the interior side of the frame wall and insulation layer. With heated interiors, vapor drive moves outward.
However, many variables come into play in modern homes designed for all seasons
and weather extremes—including modern building advances in techniques and
technologies.
The International Residential Code issues requirements according to climate
zones broken into varying classifications. In addition, state and local
building codes often give further guidance on not only whether a vapor barrier
should be installed but also where it should be placed and what the required
specs are for appropriate vapor barrier materials.
What can prove confusing is the seeming interchangeability of the terms vapor
barrier and vapor diffusion retarder. Materials that qualify as
vapor diffusion retarders are grouped into three classes that measure
permeability to moisture in perms. Class I represents the vapor barrier
category:
Class I—Actual vapor barriers have a permeability factor of 0.1 perm or less, featuring materials like glass, metal, unperforated aluminum foil, polyethylene sheets and rubber membranes.
Class II—With a range of 0.1 perm to 1.0 perm, the second class of vapor retarders includes materials like polystyrene, 30-pound asphalt-coated paper, plywood and bitumen-coated kraft paper.
Class III—This final class of vapor retarders has a broad range, from 1.0 perm to 10 perms, and includes many of the materials often used within an air barrier system—materials like gypsum board, insulation, lumber, concrete block, brick, 15-pound coated asphalt paper, latex or enamel paint, and house wrap.
Note that environmental conditions like humidity, for example, can affect some
retarders, shifting them from one class to another. Especially interesting to
note is the development of smart vapor diffusion retarders designed to limit
condensation and vapor drive in cold months when heating is necessary as well
as allow drying when air-conditioning and weather flip conditions.
Construction in Idaho’s Climate
Idaho may initially look like a simple cold-climate state on a zone map.
However, its geography offers considerable variability in conditions. Most of
the state has a dry, even high desert-like climate that extends down into
northern Nevada, but northern climes are mountainous with a good bit of winter
rain and snow from the Northern Rockies.
Matching building materials designed for optimal control of the movement of
air, heat and moisture with environmental conditions to create a home that will
withstand the tests of seasons, climate and time is actually a complex process.
If you’re ready to plan, design or build a house that will look and feel like
home, Franklin Building Supply is the perfect place to start. We have all the
materials and expertise you need.